CESAREF, Concerted European action on Sustainable Applications of REFractories, will train researchers in multi-engineering areas and expose them to the academic and non-academic sectors through international and inter-sectoral mobility combined with an innovation-oriented mind-set. They will get the right combination of research-related and transferable competences in the full production-to-the-end-of-life cycle of refractory materials applied to Iron & Steelmaking processes with regards to the new operation conditions requested by the drastic reduction of greenhouse gas emissions, improved energy efficiency, and by life cycle assessment requirements. An important part of the project will be dedicated to the sustainability of refractories, including recycling issues, using the Life Cycle Assessment methodology. 15 doctoral candidates will take advantage of the most sophisticated numerical tools and laboratory equipment to model, design and predict the life of refractory materials in critical operational conditions. Being trained in scientific, technical, and soft skills, these PhDs are the next generation of highly employable scientists and engineers in the refractory sector and related areas. New testing methods and models will be developed to address the Scientific/Technological challenges for these applications and help to design better performing and sustainable refractory materials and linings. The research training is implemented through strong relationships between 10 academia and 16 industrial partners across the EU. The CESAREF network is structured to take full advantage of intensive cooperation between academia, raw material suppliers, refractory suppliers and high-tech metal component producers with a direct link to the FIRE federation (fire-refractory.org).
Steel, cement, glass and super alloys are essential materials of our society. Steel is the most reliable material used for engineering, construction, automobile, white goods, and industrial equipment. The Iron & Steel (I&S) industry is the largest end-user of refractory products accounting for 68% of the international market. With a global steel production of 1.8 billion tons per annum and an expected growth rate of 1-1.4 % per year, the global steel demand will be around 1.9 billion tons by 2035. The apparent steel consumption in EU (28) was 168 Mt in 2018, corresponding to an average of about 328 kilograms of steel per capita per year, which highlights the importance of steel in everyday life. The competition in and out of the European territory is very intense. Imports decreased in 2020 but still held a 21 % market share. Due to rising costs related to CO2 emissions and to the European Green Deal, the urgent challenge for the industry is to stay competitive and invest in breakthrough technologies for decarbonization. The European I&S industry is a world leader in innovation, environmental sustainability and a pioneer on the development of new technical solutions to enhance resource efficiency and meet the “Net-Zero emission of Green House Gas” (GHG) target by 2050. 84 % of the European Steel producers have already committed themselves to be fully Net Zero by 2050, compared to 67 % in Japan and 19 % in China. Steel production is very highly energy intensive and accounts for 25 % of Europe’s industrial CO2 emissions and 7 % of the global industrial GHG emissions. Every ton of steel produced in 2018 emitted on average 1.85 tons of CO2. As shown in Figure 2, Net-Zero emissions by 2050 entails alternative breakthrough technologies and processes. The European I&S industry has numerous decarbonisation projects in the works, at various levels of technical readiness, either on the Smart Carbon Usage and/or the Direct Carbon Avoidance technological pathways. By dealing with energy efficiency through new refractory materials and technologies, the CESAREF network will target research topics not presently covered. Efficiency programs like EDEFU have worked on energy efficiency and reducing CO2 emissions through new furnace design. Other initiatives are dedicated to steelmaking by enlarging the use of hydrogen based-Direct Reduced Iron (DRI) as feeding material in Electric Arc Furnaces or by developing low-carbon footprint iron production technologies. The conversion from carbon-based fuels to clean burning hydrogen-based mixes is a major change in the industry. DRI is expected to be a major decarbonization lever and offers the potential for truly green steel, particularly in Europe where 70 % of steel is still produced through integrated process. However, the current refractory materials are not designed to perform as well with such new operation practices.
News
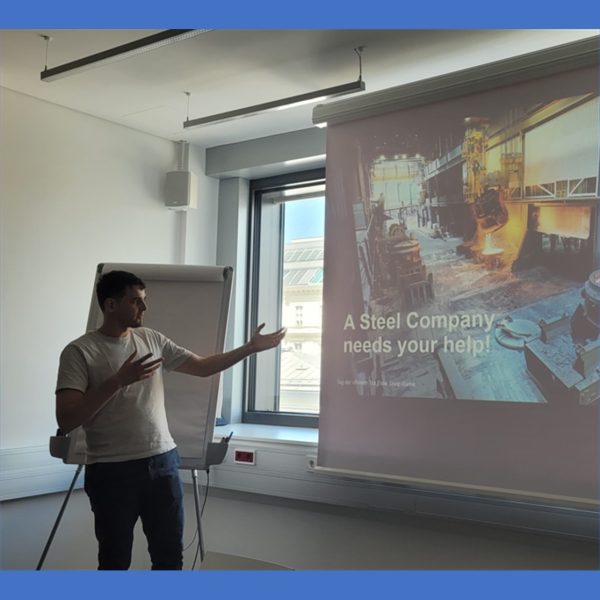
Victor Sao Paulo Ruela participates in Tag der offenen Tür at TU Wien
During the Tag der offenen Tür at TU Wien (Open day), which took [...]
Harikeshava RANGANATHAN at IREFCON
The India International Refractories Congress (IREFCON), an [...]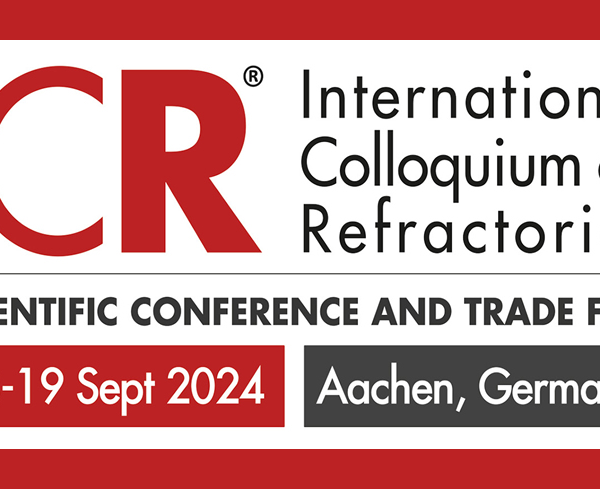